American mechanics: the most in-demand talent in the next decade
"I replaced the motor controller for Tesla Model Y and received $2,000 in overtime pay on the same day."--Alex Martinez, a 28-year-old mechanic, said this when sharing a repair video on YouTube. Driven by smart manufacturing and the new energy revolution, American mechanics are becoming a "hot commodity" in the manufacturing industry. This article will reveal: What kind of money-making code and development opportunities are hidden in this profession that requires code knowledge, machine tool operation, and rocket engine repair?
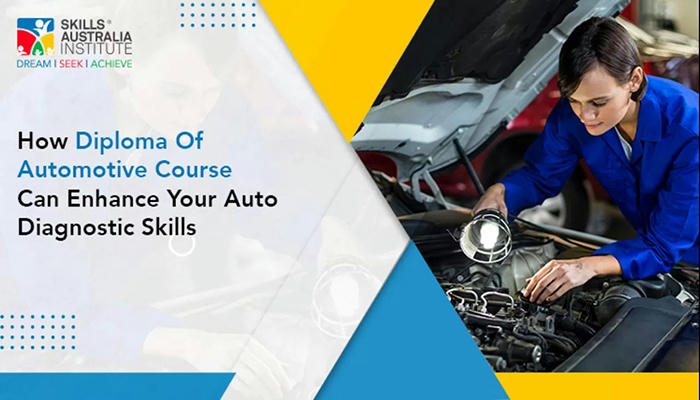
Industry trends: Demand has soared 200% in ten years
New energy vehicle revolution
In 2023, the sales of new energy vehicles in the United States exceeded 2 million, which directly led to a surge in demand for mechanics. Tesla's factory needs 30 mechanics per hour to work in shifts, and General Motors has offered an "urgent" salary of $15/h. According to BLS forecasts, by 2030, new energy vehicle maintenance positions will increase by 85%, becoming the largest growth point in the field of mechanics.
Smart manufacturing upgrade
The Boeing 787 fuselage uses more than 3,000 3D printed parts, and 90% of the maintenance at the GE aviation engine factory is completed by AI robots. However, each machine still needs 1-2 mechanics to calibrate and maintain the system. According to data from the U.S. Department of Labor, mechanics who master PLC programming and industrial robot operation earn 40% more than ordinary technicians.
Aging crisis
The average age of the U.S. manufacturing industry is 45 years old, and 20% of mechanics will retire in the next ten years. A certain auto parts factory in California even saw the spectacle of "grandfather-level" mechanics teaching their grandchildren. The scarcity of young mechanics has led to rising salaries. The starting salary for fresh graduates in a stamping workshop in Arizona has reached $22/h.
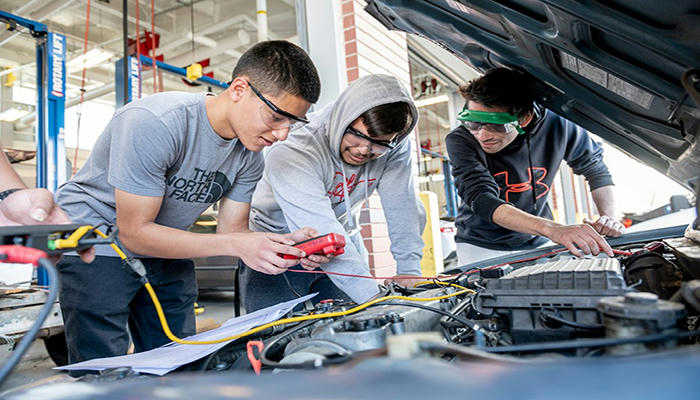
Core skills: "Hexagonal Warrior" ability of new-age mechanics
Basic skills
•Anatomical maintenance: can find the source of abnormal engine noise through a stethoscope within 15 minutes
•Precision control: use a micrometer to calibrate part tolerances (error does not exceed 0.001 inches)
•Electrical proficiency: familiar with the CAN bus system and can quickly diagnose vehicle ECU faults
Advanced weapons
•CAD/CAM programming: use SolidWorks to design customized repair fixtures
•Industrial robot operation: program KUKA robotic arms to complete precision welding (repeat positioning accuracy ±0.02mm)
•Thermal imaging analysis: locate the transmission oil leak through infrared thermal images
Certification ace
•ASE certification: American automotive service excellence certification (pass rate is only 37%)
•NCCMEB: North America's most valuable mechanic qualification certification
•OSHA 30-Hour: High-risk operation safety specification certification (mandatory requirement)
Salary and benefits: Technology is hard currency
Survival in the Novice Village
•Apprenticeship (0-2 years): 12-18/h, annual income of 25,000-36,000
•Junior technician (3-5 years): 22-28/h, annual income of 45,000-60,000
•Expert level (more than 5 years): 35-50/h + commission, annual income of 70,000-120,000+
Hidden income
•Emergency rescue: Repair factory production lines late at night, hourly wages can reach $50+ •Technical consultant: Optimize production lines for enterprises, charging 150-300 per hour •Parts sales: Use industry resources to resell scarce parts (profit margin 30%-50%)
Benefit package
•Paid training: Boeing provides $5,000 skill improvement fund each year
•Medical insurance: Most employers include dental and vision insurance
•Retirement plan: 401(k) matching rate averages 8%, and some companies provide additional IRA accounts
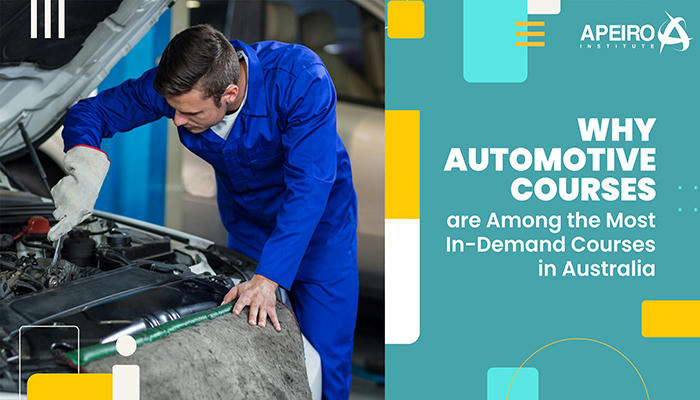
Tips for entering the industry: A five-year guide from zero to expert
Phase 1: Career enlightenment (6 months)
•Community college: Take elective courses "Mechanical Drawing" and "Welding Technology", with a practical fee of $1,500/semester
•Online courses: Udemy's "Industrial Robot Programming" certification course ($499, valid for 6 months)
•Worksite internship: Apply for the "Apprentice Partner" program through the ASE official website and accumulate 200 hours of practical experience
Phase 2: Qualification certification (3-6 months)
•ASE certification: Focus on the three core subjects of engine maintenance, transmission diagnosis, and electrical systems
•NCCMEB exam: Participate in the Phoenix Technical Institute's training class (pass rate increased to 65%)
•Safety training: OSHA 10-Hour Course (mandatory, $150/time)
Phase 3: Career Transition
•Technical Route: Mechanic → Senior Technician → Chief Engineer (Annual Salary 180,000-250,000)
•Management Route: Team Leader → Workshop Director → Factory Manager (Annual Salary 250,000-400,000)
•Entrepreneurial Route: Open a mobile repair station (average profit margin 25%), or join a chain brand (such as ASE-certified Quick Lane)
The next decade: You will witness these changes
Technology singularity
•Digital twin maintenance: GM will launch an AR maintenance system in 2025, and mechanics can "see through" the engine with Hololens glasses
•AI diagnostic revolution: Waymo's AI maintenance assistant can use voice recognition to warn of mechanical failures 300 hours in advance
•3D printed parts: Local Motors factory has achieved on-site 3D printing of 80% of repair parts, and traditional mold repairers are facing elimination
Policy dividends
•"Chips Act": $52 billion is allocated to support semiconductor manufacturing, requiring a large number of precision mechanics
•"Infrastructure Act": Rebuilding 50,000 bridges, and the demand for steel structure maintenance positions has surged
•California Environmental Protection Order: Starting in 2025, fuel vehicle repair shops must be equipped with EV charging equipment, giving rise to new mechanic positions
Career evolution
•Industrial robot engineer: annual salary of 90,000-140,000, responsible for robot maintenance and programming
•Sustainable manufacturing expert: designing zero-waste production processes, hourly wage of 45-60
•Transnational technical consultant: flying to the German Volkswagen factory to teach advanced American maintenance technology (hourly wage of $70+)
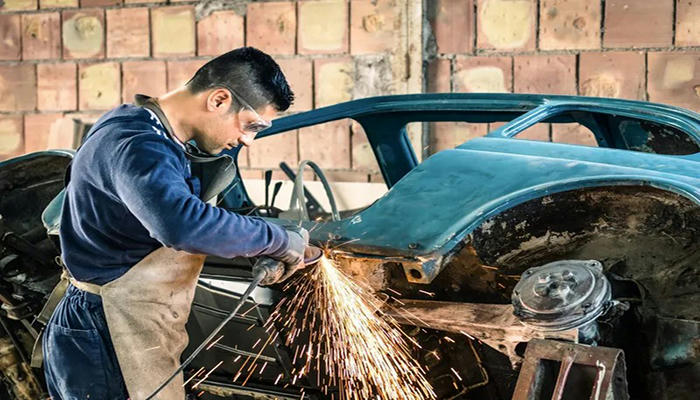
Real case: From an apprentice at a car repair shop to a technical supervisor at the Tesla factory
David Kim's career trajectory
•2018: After graduating from high school, he worked in a Korean car city and learned engine maintenance from a master
•2020: Went to the United States to obtain ASE certification and entered a Toyota 4S store in Los Angeles
•2022: With his understanding of electrification technology, he jumped to Tesla's California factory
•2023: Promoted to North American electric truck maintenance supervisor, managing a team of 15 people
•2024: Founded the TechMaster maintenance chain, valued at $2 million
Industry advice
•Continuous learning: Invest $300 per month to subscribe to "Machine Tool Technology" magazine
•Network value-added: Establish 500+ industry contacts on LinkedIn and regularly participate in ASE local chapter activities
•Risk control: Purchase $1 million/year professional liability insurance to deal with equipment damage claims
•Technical reserves: Industrial Internet of Things (IIoT) certification is required from 2025, and NCCMEB has started a pilot